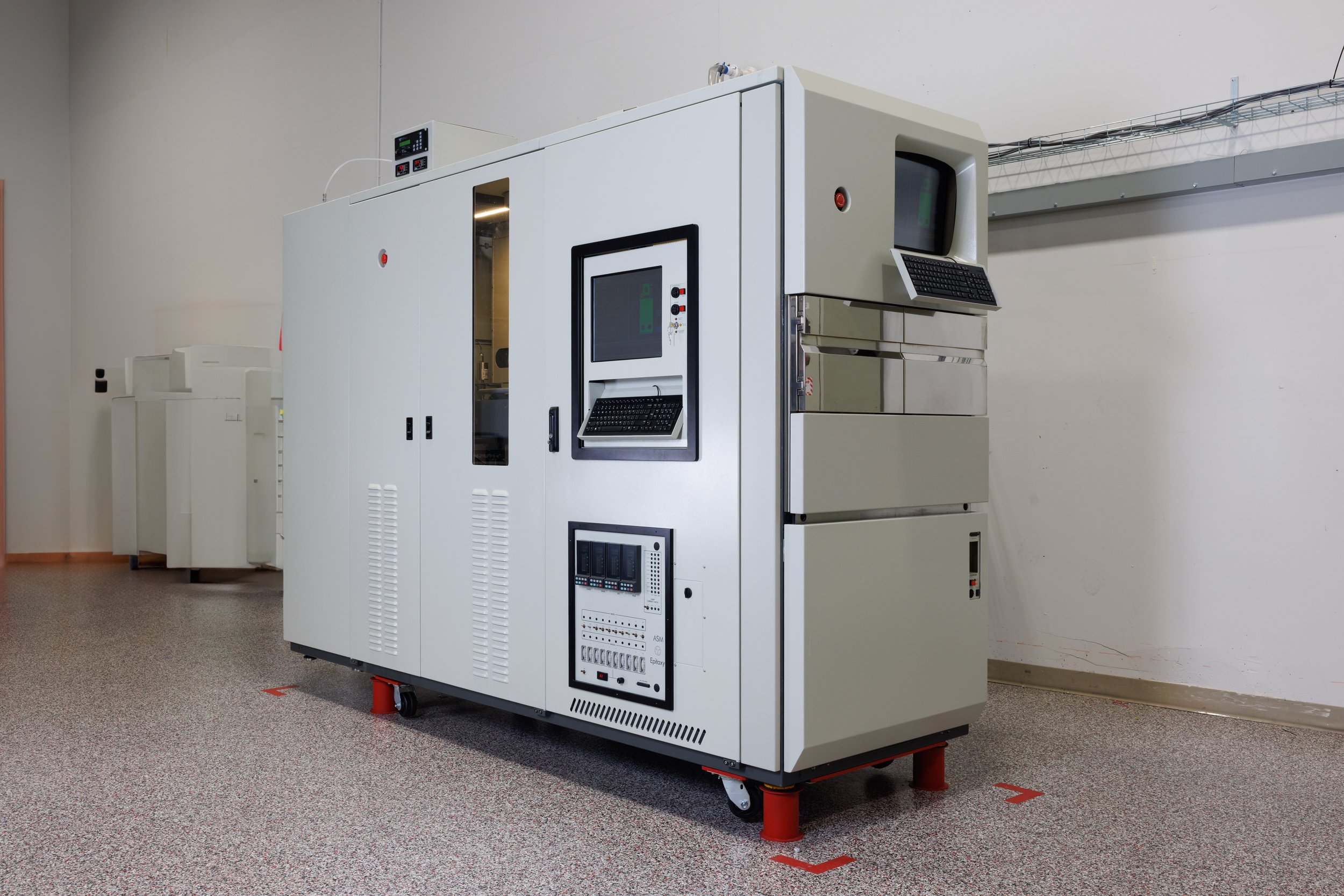
Remanufactured Tools
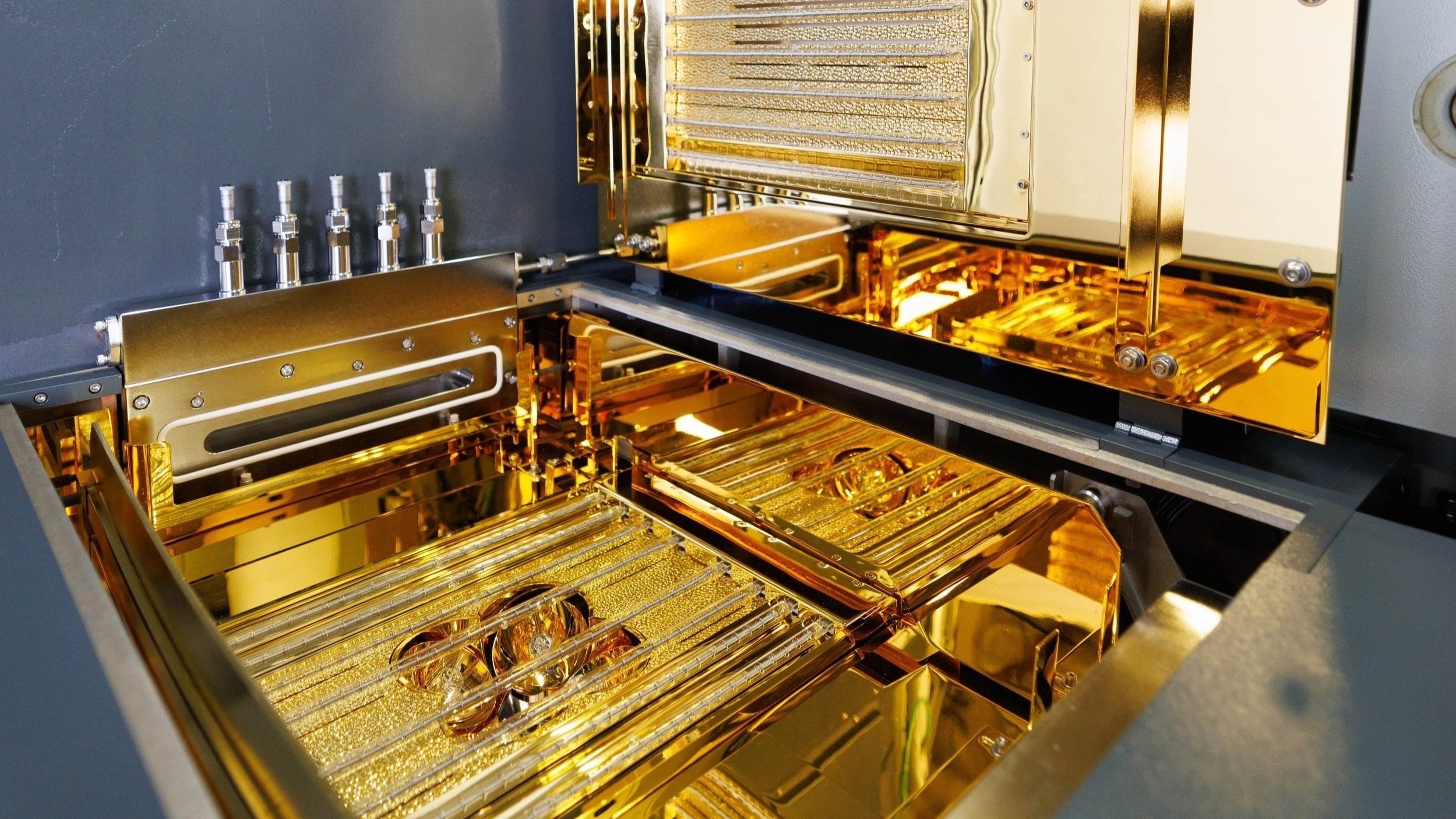
the process of remanufacture
Start from the beginning
Working with equipment brokers and end users directly, Saxony Thermal purchases the best cores we can find. Normally we have cores in stock, if we don’t we’re aware of several on the market and can have them delivered quickly.
Every tool of the over 30 we’ve remanufactured goes almost all the way down to the frame. We call this “Core Preparation” It’s not for the faint of heart. It’s a procedure we have developed over the years.
All the pneumatic lines are removed, system controller, terminal blocks and all of the cables. The outer panels that will be reused will be sent out to be stripped and recoated.
If the core tool has rust issues with the frame (many do), this is delt with during this stage.
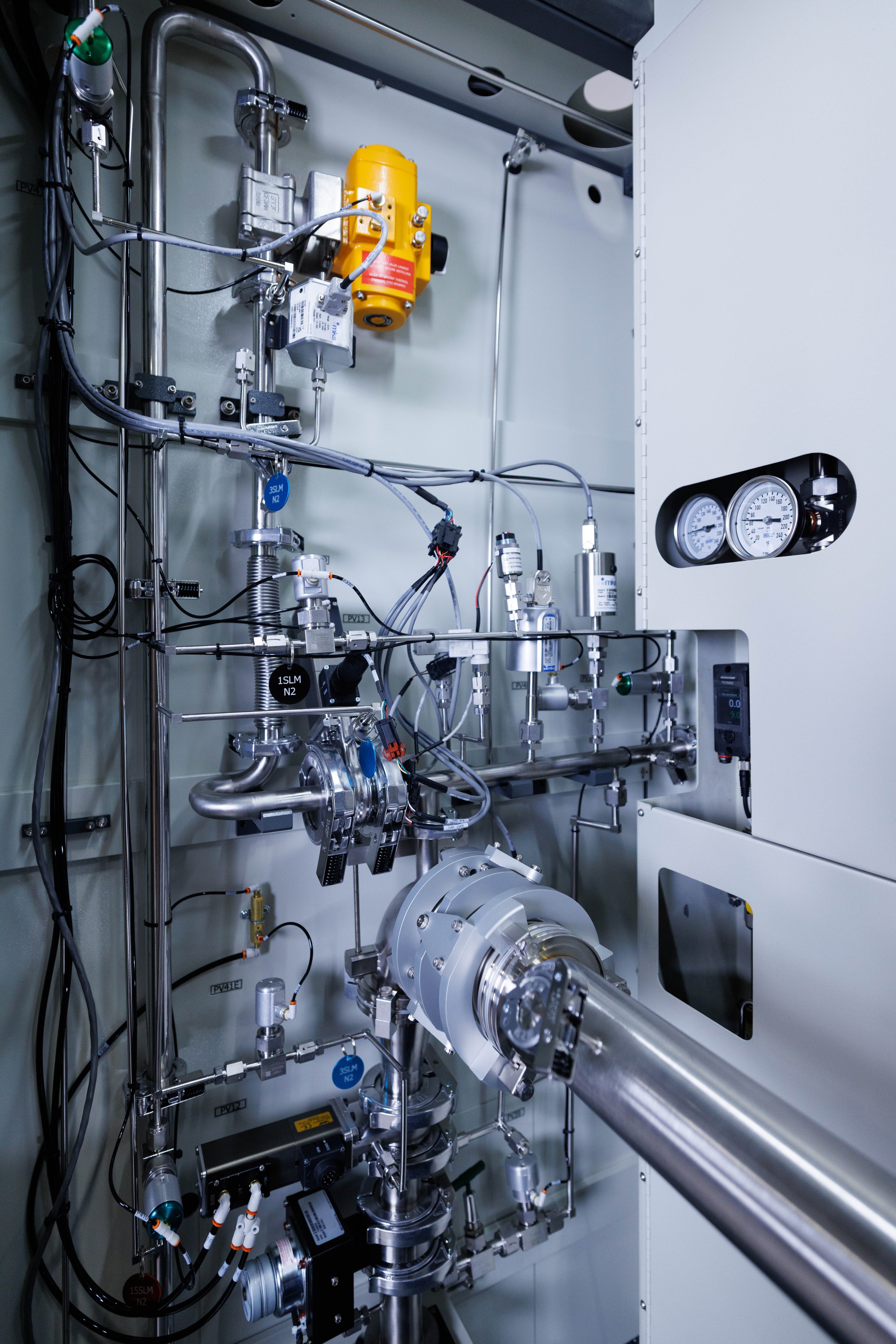
module building
from our collection of modules
Just as any OEM would, we have pre-built new modules for these tools.
These modules are built with all new components, tested individually and staged to be installed in the prepared core. You can find a collection of available modules for your own project on our modular refurbishment page. Some of the modules we’ll install are:
Gas Panel - New from the frame up
Process Chamber Enclosure - All new including the reflectors
Air Cooling
Water cooling
Wafer Rotation and Lift
System Controller
H2 Detection Upgrade
LCD Monitor Upgrade
Reduced Footprint Door
Temperature Controller Upgrade
Compumotor Upgrade
Those are the highlights, but there’s so much more
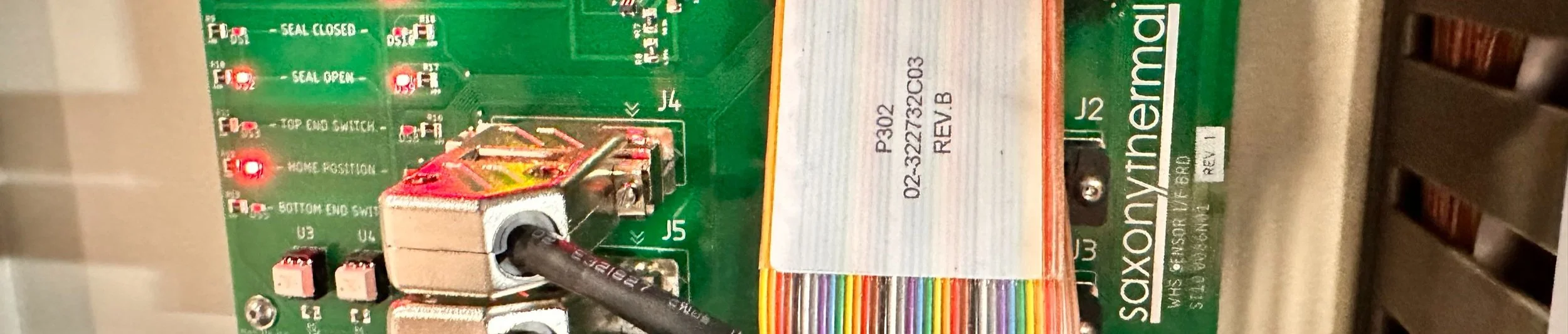
module installation
it all comes together
Once all the modules are ready for installation we get started. This is a rather quick phase since all our new cables and pneumatic connections are installed and waiting in the correct position after the core preparation phase.
Special tools and procedures we’ve developed over the years are handy here.
Every wire, cable and fitting are checked to prepare the tool for its final phase in the process.
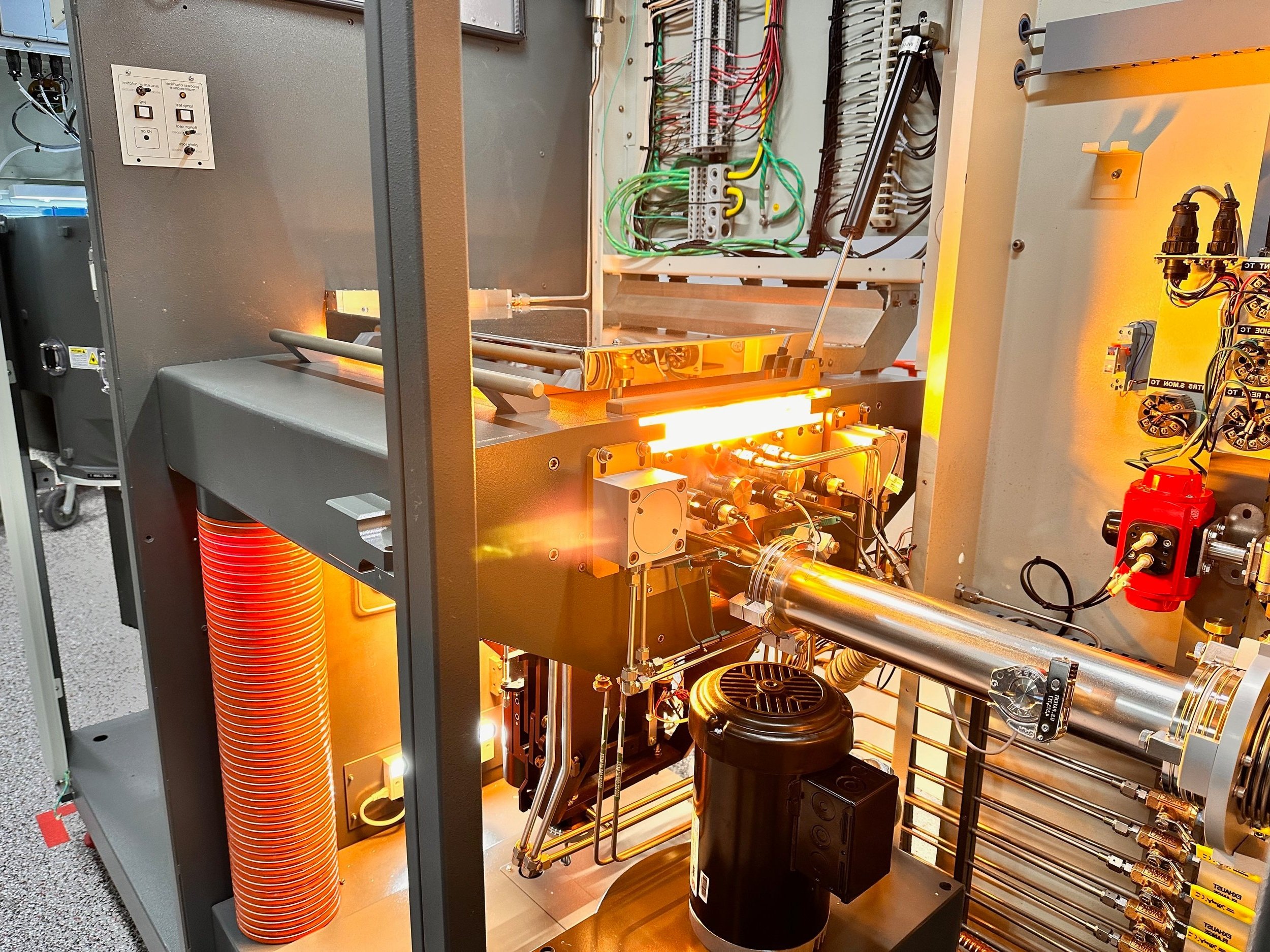
final test
Time to show off
Every tool that Saxony Thermal remanufactures goes through the paces. We want you to know that these tools will perform to your high standards. We run the tool up to 1200C in argon, cycle 100 wafers minimum, vacuum and helium leak test, test safety inputs and outputs and all the other installed systems.
Our final test procedure is 250 steps. We skip nothing. We are going to ensure that when our field service staff arrives on your site to install this tool the project will run smoothly.